Air Compressor Size for an Industrial Finish Nailer
Industrial finish nailers are indispensable tools for professionals in woodworking, cabinetry, and trim installation. Their precision and efficiency rely heavily on a properly sized air compressor to deliver consistent power. Choosing the right compressor size for an industrial finish nailer can be challenging, as it involves balancing airflow, pressure, tank capacity, and application demands. This guide provides an in-depth exploration of the factors influencing compressor selection, ensuring optimal performance for your finish nailer while avoiding common pitfalls. With practical insights, technical specifications, and real-world considerations, this article equips you with the knowledge to make an informed decision.
Why Choose Pneumatic Finish Nailers?
Pneumatic finish nailers offer distinct advantages over their cordless counterparts, making them a preferred choice in industrial settings:
- Lightweight and Compact: Pneumatic nailers are typically lighter (around 4 lbs for 16-gauge models) compared to battery-powered models (often exceeding 6 lbs), reducing user fatigue during extended use.
- Consistent Power Delivery: Unlike cordless nailers, which lose power as batteries deplete, pneumatic nailers maintain steady performance as long as the compressor supplies adequate air.
- Cost-Effective: Pneumatic nailers are generally less expensive upfront and require no battery replacements, lowering long-term costs.
- Durability: With fewer moving parts and no battery-related components, pneumatic nailers are robust and suited for heavy-duty industrial use.
However, these benefits depend on pairing the nailer with a compressor that meets its air requirements. An undersized compressor can lead to insufficient power, while an oversized one may be unnecessarily costly and cumbersome.
Understanding Finish Nailers and Their Air Requirements
Finish nailers are specialized tools designed for precision tasks, such as installing trim, assembling cabinetry, or attaching molding. They typically use 15-gauge or 16-gauge nails, which require less force than the larger nails used in framing or roofing applications. Key specifications for pneumatic finish nailers include:
- Pressure (PSI): Most finish nailers operate effectively between 70 and 120 PSI, with 90 PSI being a common target for optimal performance. Operating below 70 PSI may result in incomplete nail penetration, while exceeding 120 PSI risks damaging the tool or workpiece.
- Airflow (CFM): Cubic feet per minute (CFM) measures the volume of air the nailer consumes. A typical 16-gauge finish nailer requires approximately 4.5 CFM at 90 PSI for intermittent use. However, this varies by model, so always consult the manufacturer’s specifications.
- Duty Cycle: Finish nailers are generally used intermittently, firing nails in short bursts rather than continuously. This impacts compressor selection, as intermittent use requires less airflow than continuous-use tools like sanders.
To illustrate, here’s a sample specification for a popular industrial finish nailer:
Nailer Model | Nail Gauge | PSI Range | CFM at 90 PSI | Weight |
---|---|---|---|---|
Senco FinishPro 16XP | 16-gauge | 70–120 PSI | 4.5 CFM | 4.2 lbs |
Always verify the CFM and PSI requirements of your specific nailer model, as these values guide compressor selection.
How Air Compressors Work
An air compressor is essentially a pump that pressurizes air and stores it in a tank (or receiver) for use by pneumatic tools. Here’s a simplified overview of its operation:
- Compression: The compressor’s motor drives a piston or screw mechanism to compress air, increasing its pressure.
- Storage: The compressed air is stored in a tank, typically measured in gallons (e.g., 2–12 gallons for portable compressors).
- Delivery: When the nailer is activated, air is released from the tank through a hose and pressure regulator, powering the tool.
- Recharge: As the nailer consumes air, tank pressure drops. When it falls below a set threshold, the compressor motor restarts to replenish the tank.
The compressor’s ability to maintain adequate pressure and airflow depends on its horsepower (HP), tank size, and design. For finish nailers, portable compressors are most practical due to their size and mobility.
Types of Portable Compressors
Portable compressors come in several configurations, each suited to different applications:
Compressor Type | Tank Size (Gallons) | Typical CFM at 90 PSI | Best For |
---|---|---|---|
Hotdog/Pontoon | 2–3 | 4–6 CFM | Small jobs, single nailer |
Pancake | 4–6 | 5–7 CFM | General woodworking, multiple tools |
Twin-Stacked | 4–6 | 6–8 CFM | Heavy-duty tasks, frequent use |
Wheelbarrow | 8–12 | 8–12 CFM | Large projects, multiple tools |
Note: Tank size does not directly correlate with CFM, as CFM depends on the compressor’s motor and pump efficiency. However, larger tanks allow longer operation before the compressor needs to recharge.
Key Factors in Compressor Selection
Selecting the right compressor for an industrial finish nailer involves balancing several factors:
1. Airflow (CFM) Requirements
The CFM rating of the compressor must exceed the nailer’s requirements to ensure consistent performance. For a 16-gauge finish nailer requiring 4.5 CFM, a compressor delivering at least 6–7 CFM at 90 PSI is recommended. This 50% buffer accounts for inefficiencies, such as air leaks or pressure drops over long hoses, and supports intermittent use without frequent recharging.
Pro Tip: To calculate the minimum CFM, multiply the nailer’s CFM by 1.5 (e.g., 4.5 CFM × 1.5 = 6.75 CFM). This ensures the compressor can handle peak demands.
2. Pressure (PSI) Capabilities
The compressor must maintain a stable pressure within the nailer’s PSI range (70–120 PSI). Most portable compressors deliver up to 135–150 PSI, which is sufficient for finish nailers. However, ensure the compressor includes a reliable pressure regulator to fine-tune output to the nailer’s optimal PSI (e.g., 90 PSI).
3. Tank Size and Duty Cycle
Tank size affects how long the compressor can supply air before recharging. For finish nailers used intermittently, a 4–6-gallon tank (pancake or twin-stacked) is typically adequate. For continuous or high-volume tasks, a larger 8–12-gallon tank (wheelbarrow) may be necessary to minimize recharge cycles.
The duty cycle—how frequently the nailer is used during a workday—also influences tank size and compressor power:
- Light Duty: Occasional use (e.g., small trim projects) requires a smaller tank (2–4 gallons) and lower horsepower (1–2 HP).
- Moderate Duty: Regular use (e.g., cabinetry assembly) benefits from a 4–6-gallon tank and 2–3 HP.
- Heavy Duty: Near-continuous use (e.g., large-scale installations) demands an 8–12-gallon tank and 3–5 HP.
4. Multiple Tool Support
If you plan to power multiple tools simultaneously (e.g., a finish nailer and a brad nailer), sum the CFM requirements of all tools. For example:
Tool | CFM at 90 PSI |
---|---|
Finish Nailer | 4.5 CFM |
Brad Nailer | 2.0 CFM |
Total | 6.5 CFM |
In this case, a compressor delivering at least 9–10 CFM (6.5 × 1.5) is ideal. However, if tools are used intermittently, a slightly lower CFM may suffice, as simultaneous peak demand is unlikely.
5. Portability and Power Source
For contractors working across job sites, portability is critical. Pancake and hotdog compressors are lightweight (30–60 lbs) and easy to transport. Wheelbarrow compressors, while heavier (100–200 lbs), offer greater capacity for demanding projects. Most portable compressors run on standard 120V outlets, but ensure your job site has adequate power.
6. Noise Levels
Industrial environments can be noisy, but quieter compressors (60–75 dB) improve working conditions. Look for models with noise-reducing features, such as oil-lubricated pumps or insulated tanks, especially for indoor use.
Recommended Compressor Specifications
Based on the typical requirements of a 16-gauge industrial finish nailer, here are recommended compressor specifications:
Feature | Specification |
---|---|
CFM at 90 PSI | 6–8 CFM |
PSI Range | 100–150 PSI (with regulator) |
Tank Size | 4–6 gallons (pancake or twin-stacked) |
Horsepower | 2–3 HP |
Weight | 30–80 lbs (for portability) |
Noise Level | 60–75 dB |
Example Compressors
Here are three compressors suitable for industrial finish nailers, with specifications and approximate prices:
Model | CFM at 90 PSI | Tank Size | PSI | HP | Weight | Price (USD) |
---|---|---|---|---|---|---|
DeWalt DWFP55126 | 6.0 CFM | 6 gallons | 165 PSI | 2.5 HP | 30 lbs | $200–$250 |
Makita MAC2400 | 8.4 CFM | 4.2 gallons | 130 PSI | 2.5 HP | 77 lbs | $350–$400 |
California Air Tools 8010 | 6.0 CFM | 8 gallons | 120 PSI | 2.0 HP | 54 lbs | $300–$350 |
Note: Prices are approximate and may vary by retailer or region. Check for current pricing and availability.
Visualizing Compressor Selection
To aid decision-making, the following Mermaid flowchart outlines the process of selecting a compressor for an industrial finish nailer:
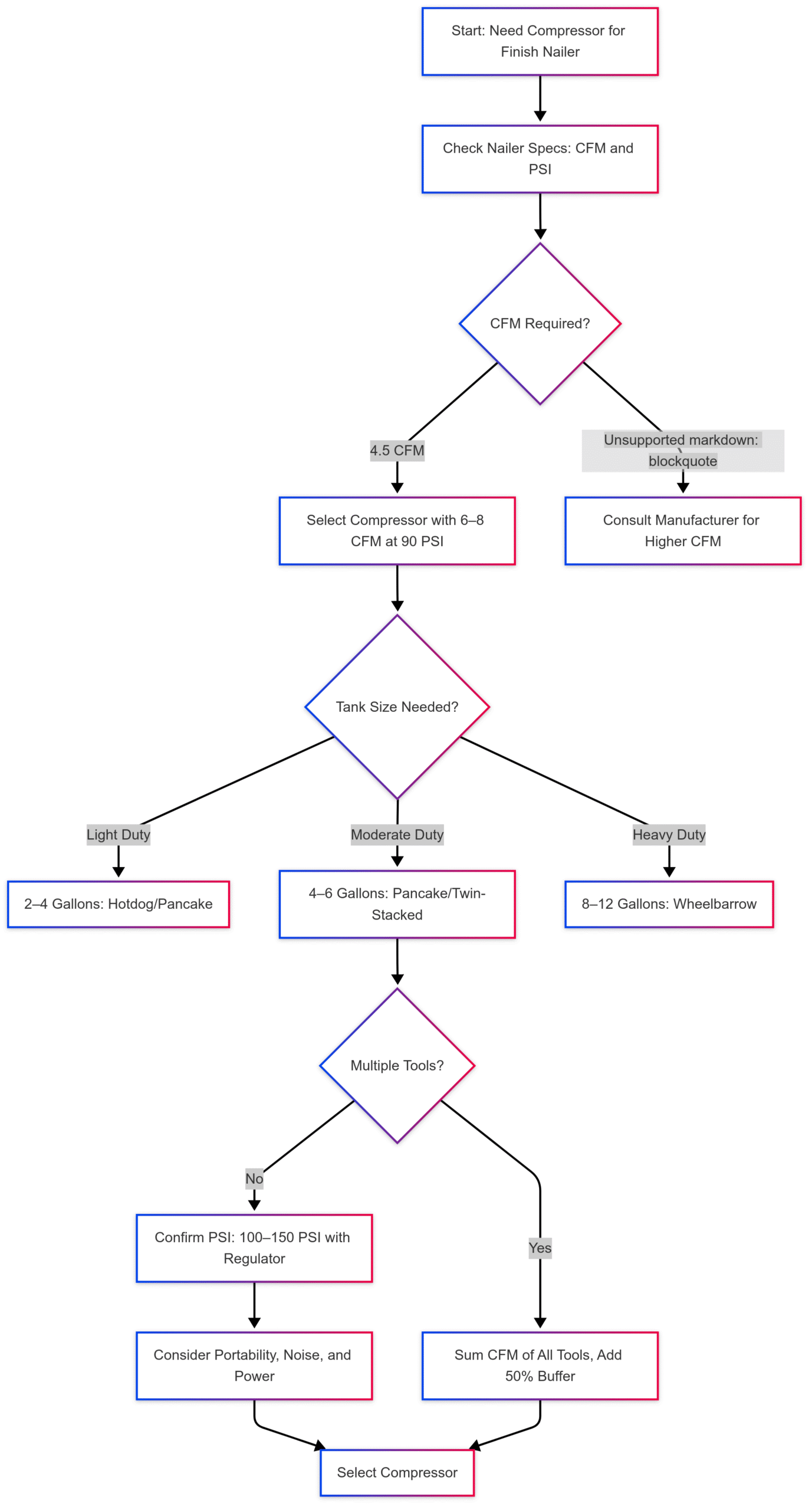
Visualizing Compressor Selection
This flowchart ensures you account for CFM, tank size, multiple tools, and practical considerations like portability.
Practical Tips for Optimal Performance
To maximize the performance of your finish nailer and compressor, follow these best practices:
- Test on Scrap Material: Before starting a project, test the nailer on a scrap piece of the same material. Adjust the PSI gradually (starting at 70 PSI) until nails drive flush without over-penetration.
- Use a Pressure Regulator: Install an in-line regulator near the nailer to maintain consistent PSI, especially when using long hoses (e.g., 50 feet), which can cause pressure drops.
- Check for Leaks: Inspect hoses and fittings for leaks, as even small leaks can reduce CFM and pressure, affecting performance.
- Maintain the Compressor: Drain the tank daily to remove moisture, check the air filter regularly, and lubricate oil-lubricated models per the manufacturer’s instructions.
- Match Fittings: Ensure air hoses and couplers match the compressor and nailer (e.g., 1/4″ or 3/8″ NPT fittings) to prevent airflow restrictions.
- Adjust for Material Density: Softer woods (e.g., pine) require lower PSI (70–80), while hardwoods (e.g., oak) may need higher PSI (90–100).
Troubleshooting Common Issues
If your finish nailer isn’t performing as expected, consider these common issues and solutions:
Issue | Possible Cause | Solution |
---|---|---|
Nails not driving flush | Insufficient PSI | Increase PSI gradually, test on scrap |
Nails driven too deep | Excessive PSI | Reduce PSI or adjust depth control |
Inconsistent nail driving | Pressure fluctuations or leaks | Check regulator, hoses, and fittings |
Compressor runs continuously | Undersized compressor or high duty cycle | Upgrade to higher CFM or larger tank |
Nails bending or jamming | Incorrect PSI or nail type | Verify PSI and use recommended nails |
Safety Considerations
Pneumatic nailers and compressors pose risks if mishandled. Follow these safety guidelines:
- Wear Protective Gear: Use safety glasses, gloves, and a helmet to protect against flying debris or nail ricochets.
- Disconnect Air Hose: Unplug the hose when not in use, during maintenance, or when clearing jams.
- Avoid Bypassing Safety Features: Never disable the nailer’s safety tip or trigger mechanism.
- Check Compressor Stability: Ensure the compressor is on a stable surface to prevent tipping.
- Follow Manufacturer Guidelines: Adhere to recommended PSI and maintenance schedules to avoid tool damage or injury.
Pneumatic vs. Cordless Finish Nailers
While this guide focuses on pneumatic finish nailers, it’s worth comparing them to cordless models to understand their trade-offs:
Feature | Pneumatic | Cordless |
---|---|---|
Power Consistency | Steady with adequate compressor | Decreases as battery depletes |
Weight | Lighter (4–5 lbs) | Heavier (6–8 lbs) |
Portability | Limited by hose and compressor | Fully portable, no hose |
Cost | Lower upfront, no battery costs | Higher upfront, battery replacements |
Maintenance | Compressor maintenance required | Minimal, but battery care needed |
For industrial settings with access to power and space for a compressor, pneumatic nailers are often the better choice due to their reliability and cost-effectiveness.
FAQs
The ideal PSI ranges from 70 to 100 PSI, depending on the nailer model and material. Start at 70 PSI and adjust upward until nails drive flush.
Yes, a 2–6-gallon compressor with 6–8 CFM at 90 PSI is sufficient for most finish nailers used intermittently. For heavy-duty tasks, consider a larger tank.
An undersized compressor may not deliver enough CFM or PSI, causing nails to drive inconsistently or not at all. The compressor may also run continuously, leading to overheating.
Yes, but sum the CFM requirements of all nailers and add a 50% buffer. For example, two nailers requiring 4.5 CFM each need a compressor with at least 13.5 CFM.
Drain the tank daily, check the air filter monthly, lubricate oil-lubricated models as recommended, and inspect hoses and fittings for wear.
Conclusion
Choosing the right air compressor for an industrial finish nailer is critical to achieving professional results in woodworking and trim installation. By understanding the nailer’s CFM and PSI requirements, selecting a compressor with adequate airflow and tank capacity, and considering factors like duty cycle and portability, you can ensure consistent performance and efficiency. Opt for a compressor delivering 6–8 CFM at 90 PSI with a 4–6-gallon tank for most applications, and always test settings on scrap material to fine-tune performance. With proper selection, maintenance, and safety practices, your pneumatic finish nailer and compressor will be a reliable duo for any industrial project.
Please share this Air Compressor Size for an Industrial Finish Nailer your friends and do a comment below about your feedback.
We will meet you on next article.
Until you can read, KitchenAid Ice Maker Red Light Blinking Twice